
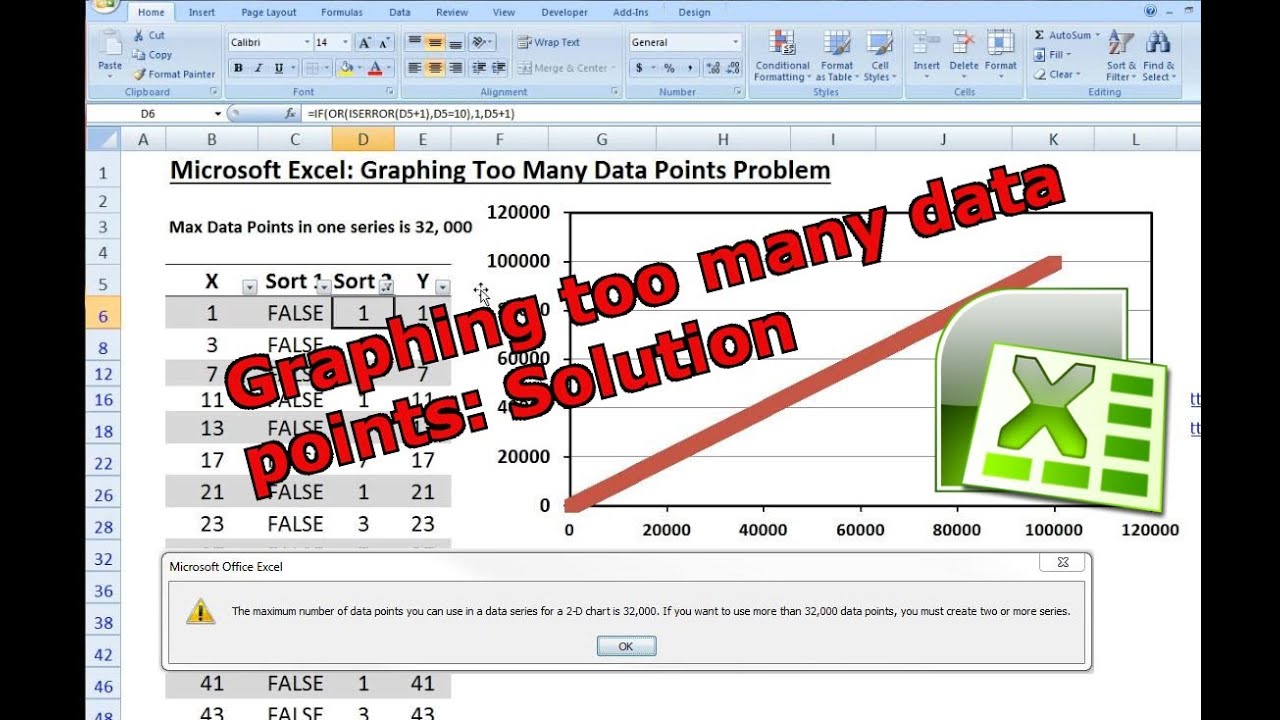
I simplified my picture compared to the actual part and unfortunately I don't have probing capabilities on that hole. Hoedeman I'm sorry I should have mentioned that I can't even probe the hole. Then level to "A", rotate to "B", set "Z" origin to "A", set "Y" origin to "B" and set "X" origin to the point from the line/plane intersect. 225 in your picture, construct a plane to the alignment, then level to the "B" plane, offset by whatever value they want, then construct a plane to the alignment, then intersect the "A" offset plane with the measure "C" plane, giving a line, the intersect that line with the offset "B" plane. THEN you would have to level to the "A" plane, offset the alignment by the. If they want a point where the hole goes for a gage point, but don't want the hole used, then they have to decide WHICH they want, if there is no surface (due to a hole) then they can't use that as a gage point.ĪS FOR 'constructed' feature method, measure the 3 planes. You have to use 3 sample hits for a hole anyway to use it in an iterative alignment, and those 3 surface sample hits also make it a surface point, BUT, the actual point would be the center of the hole (cylinder) where it intersects the surface. You can still use the 'hole' sort of, if that is where they want the point. Do you think it can be done with a traditional alignment with constructions features like I did instead? So, an iterative alignment wouldn't work if they decide to do that. There was talk about the Y and Z basic values being where a thru hole pierces the angled surface (but they don't actually want to use the thru hole for the alignment). I'm confident that I could figure it out but. Oof.I have little experience with iterative alignments. Set it to measure all always and it will cycle through twice measuring all the hits.Thank you. Iterative alignment, "A" hits for level, "B" hits for rotate, and the one hit on the "C" for origin. You should be able to use ITERATIVE alignment to get that, let it cycle thru the alignment and it should get the depth right, and for the "y" value, you simple use that for the point.ġ hit on the "C" surface at the correct depth, using the correct vector, and using whatever they want for the "Y" value ('depth' to the 'b' surface) I tried offsetting the alignment in the Y axis, and that didn't change the Y value of my resulting point. A basic Y dimension from plane B (the front face). Now, lets say the designer throws in another basic dimension. I just want to verify that I did all of that right This looks like it places the point where I want it. I believe this creates a plane parallel to A at -.225Ĭonstruct projection point and select the above constructed plane and the angled planeįinally, translate my X to the new constructed point Probed a temporary tertiary datum, and translated my X to itĬonstruct Plane -> selected PLN_A -> Offset -> clicked "Offsets." -> clicked "Calculate offsets" -> Input the values 0,0,-.225 0,0,1.
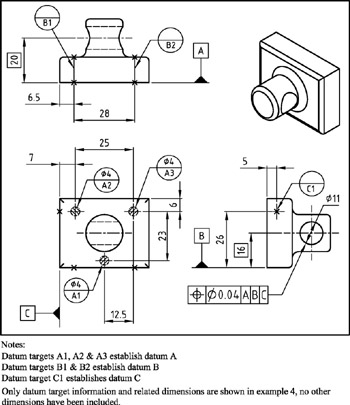
Probed plane B (front face of part) - rotated and translated my Y- to it Probed plane A - leveled and translated my Z+ to it Now the tertiary datum is a "gage point" (I think that's what people call it) on an angled surface, at a basic distance from A. The secondary datum (B) is the front face of the part. Here is the scenario I am stuck with: The primary datum (A) is the top plane. Unfortunately, they opted not to take this advice. So I recommended that the designer that they use perpendicular datums or at least an intersection point of two physical features. I just want to make sure I did this right, and I have an additional question.
#Datum points manual#
When taking the center of the component as the origin, the two datum points are required to be symmetrical (as shown in Figure 10).I hope someone doesn't mind helping me with this because unfortunately I have no way of verifying this program through manual measurements. It is necessary to place local reference points for wing pin packaging devices with pin spacing less than or equal to 0.4mm and face array packaging devices with pin spacing less than or equal to 0.8mm. If the four edges cannot be satisfied, the transmission edge must at least meet the requirements. The distance between the center of the reference point and the edge of the plate must be greater than 6.0 mm. The number of datum points is 3, which is distributed in the shape of “L” on the edge of the plate, and the distance between the datum points is as far as possible. When mirror symmetry is used, the reference points on the auxiliary side need to meet the requirement of overlap after flipping. See Figure 9 for the location requirements of the reference point. It is distributed in the shape of “L” on the edge of the plate. There are three reference points for plate making and three for unit.

Make-up needs to place make-up reference point and unit reference point.
